The next big digital revolution is happening in pharma industry
Digital revolution is all about creating seamless connectivity between machines, processes, and people within and beyond manufacturing facilities to increase quality, productivity and profit from the power of advanced data analytics
The Indian pharma industry offers tremendous opportunities for the automation sector. With globalisation and competitive market demands, more companies are becoming open to digitalisation as it is being used in many pharmaceutical processes, from drug discovery to manufacturing to packaging. On top of that, compliance with regulatory requirements opens new opportunities and challenges for automation suppliers.
Digital revolution is all about creating seamless connectivity between machines, processes, and people within and beyond manufacturing facilities to increase quality, productivity and profit from the power of advanced data analytics. With these next-generation automation solutions, pharma manufacturing companies can digitise their operations, increase efficiencies, enhance product quality, and fulfill regulatory compliances.
Pharma companies are usually tasked with examining data at every stage of their manufacturing process, right from the time raw materials arrive until the final product is packed and sent for distribution. In traditional pharmaceutical facilities, the references and information about drug formulation, production, equipment and data of QA-QC are manually entered in data sheets, which are prone to human errors and can even be manipulated. With such non-real-time information, it is difficult for management to take corrective actions and make timely decisions. However, with connected plant and Industrial IoT (IIoT) solutions, manufacturers can access data in real-time to monitor production, quality, OEE and equipment condition. It also enables mass customisation and batch size with cost-effective production.
Improved operational efficiencies
With IIoT, manufacturing facilities can monitor data from shop floors in real-time, enhancing process efficiencies. In the pharma industry, appropriate quality assurance is important. Without it, companies cannot guarantee that the product conforms to necessary quality and safety standards. Many times, product quality suffers because of machine downtime. In such cases, monitoring the conditions of assets in real-time can help in increasing equipment availability, preventing unplanned downtime.
Monitoring solutions like condition monitoring can predict device failures using real-time data helping scheduling services. Energy monitoring provides us with real-time data of the energy consumption and various other vital electrical parameters for a particular machine or process. All these data are collected from a machine or shop floor into the supervisory and control system to help us enable maximum life cycle usage of a product, maximising machine uptime resulting in improved OEE. Management can make faster and more intelligent business decisions using real-time data of operational insights. IIoT helps prioritise business decisions to reduce operating costs.
B&R’s condition-monitoring modules reliably detect potential maintenance issues and are extremely easy to configure. A unique feature of these modules is that they perform vibration analysis locally. The availability of fully processed results minimises the time and cost of integration. These results also provide detailed insight into the system mechanics, allowing existing processes to be optimised with maximum efficiency.
B&R’s energy-monitoring modules precisely measure all essential electrical parameters as configured. Often, it’s not only the measured value that is important, but also the exact moment when a group of measured values is read out. The module is equipped with a NetTime timestamp function which supplies a timestamp for the recorded position and trigger time with microsecond accuracy. Later, these values can be analysed as per requirements, and energy cost can be optimised, which will lead to an energy-efficient system.
Inter-connected machines or processes on the shop floor provide a massive amount of important data. B&R’s PharmaEdge solution can easily collect the data. PharmaEdge is an integrated, out-of-the-box, optimised offering from B&R for the pharma industry to meet the increasing demand of FDA compliance. It helps achieve cyber-security and advanced detailed reporting, analytics and business intelligence functionality. PharmaEdge offers all benefits of SCADA and a robust control system in one device. The possibility of adding energy monitoring, condition-based predictive maintenance, and MES/ERP connectivity enables smart and futuristic machines.
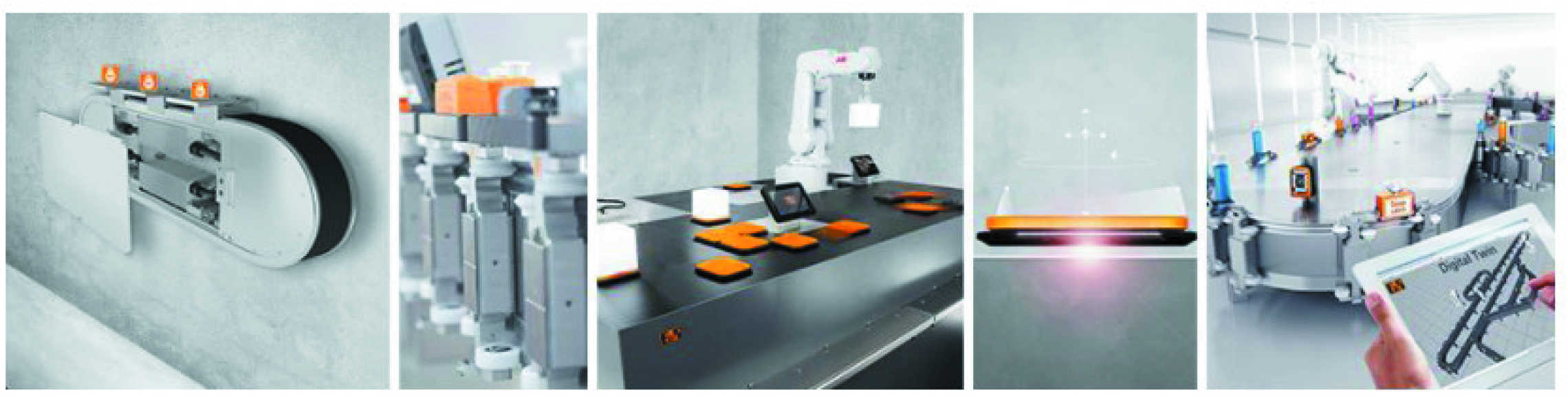
Digital remote access
Indian pharma OEMs are selling their machines, equipment and systems worldwide. Modern communication is helping to bring distant locations closer. However, for OEMs, having customers worldwide also comes with its share of new challenges. The situation becomes even complex during periods of extensive maintenance and unplanned downtimes. OEMs increasingly rely on remote maintenance to avoid incurring travel costs of service technicians and engineers worldwide. Remote maintenance makes connectivity, diagnosis and maintenance easier than ever and improves after-sales service. Service technicians can access machines from anywhere in the world. The secure remote maintenance solution utilises the latest IT and security standards and provides significant savings with low investment costs.
The new remote maintenance solution from B&R makes diagnosis and maintaining machinery and equipment easier and secure. The solution utilises the latest IT and security standards, enabling significant savings with low investment. With B&R’s remote maintenance solution, a service technician can access machines from anywhere in the world to retrieve logbook entries, application data, and much more. When a customer’s equipment or machine is not working, every minute counts, and there is immense pressure on maintenance and production teams to get the machine up and running. If a service technician is not available on-site, with B&R’s remote maintenance solution, a technician can connect, diagnose, adjust parameters, and resolve errors – all in a matter of moments.
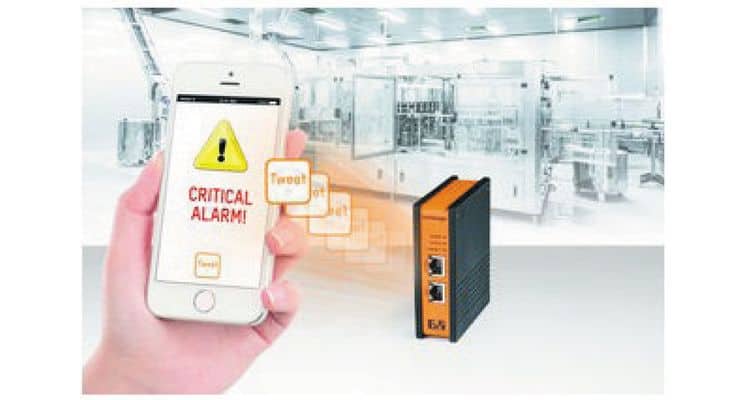
Enabling mass customisation
Demand for individualisation is creating new business opportunities. However, while executing this, a high ratio of setup costs to unit production costs acts as a bottleneck in the manufacturing process. Next-generation innovative mechatronic systems deliver key advantages for advanced manufacturing solutions. The flexible, operator-friendly conveyors make production more efficient while improving product quality. This makes the production line more economical and effective at any volume from mass production down to batch size one.
B&R’s innovative mechatronic systems ACOPOStrak, SuperTrak and ACOPOS 6D, help achieve increased demand effectively and efficiently. These systems can be fully integrated into any machine, which reduces the overall footprint of the line and improves processing precision. B&R’s next-generation industrial transport systems can be implemented up to IP69K with dust and water protection and smooth surfaces easy to clean. The hygienic design certifies operation in food grade environment. The industrial-grade design ensures high availability and reliability with 24/7 operation. The mechatronic systems synchronise with robotics and CNC systems to create integrated production lines. This helps to make the production and packaging lines economical and effective at any volume from mass production down to batch size one. These systems allow products to be transported flexibly and independently and then grouped at a station to be processed as a batch. Overall, the production process can be accelerated by up to 50 per cent for a significant boost in productivity. B&R’s smart-factory motion control in transport technology helps achieve key advantages: maximum availability, high-speed transport and positioning, rapid changeover, and fault-tolerant high quality.
B&R’s innovative mechatronic systems boost the Overall Equipment Effectiveness (OEE), multiply the Return On Investment (ROI), and accelerate the Time To Market (TTM).
IIoT is currently in its nascent stages of adoption and started gaining interest in the Indian pharma industry, but its eventual impact across the global pharma sector is indisputable. IIoT helps in the standardisation of the manufacturing process along with data integrity. By systematically monitoring and analysing large volumes of data, manufacturers can benefit from improved production efficiency, productivity, reliability and quality. IIoT provides manufacturers with a holistic view of production, raw materials and distribution, leading to better and feasible analysis of the processes, thereby increasing operational efficiency.
- Advertisement -